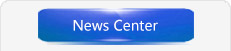
- The process flow of ...2025/5/6
- Review of the Textil...2025/5/6
- What is the market p...2025/4/21
- Breakthroughs in the...2025/4/21
- A delegation of youn...2025/4/15
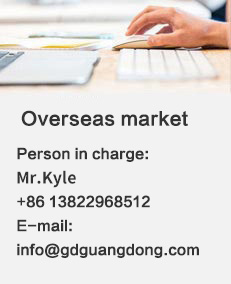
The process flow of polypropylene FDY network filament!
The technological process of polypropylene FDY (fully drawn filament) network filament mainly includes the following steps:
Slice and dry
Polypropylene chips usually contain a certain amount of moisture. If not removed, it will cause polymer degradation during the spinning process and affect the quality of the fibers. Therefore, the first step is to dry the polypropylene chips to reduce their moisture content to a certain extent, generally requiring a moisture content of less than 0.05%. Commonly used drying equipment includes hot air circulation drying ovens, vacuum drying ovens, etc.
Melt extrusion
The dried polypropylene chips are sent into the screw extruder, where the chips are heated to a molten state. The melting point of general polypropylene is around 165-175℃.
The screw extruder pushes the slices forward through the rotation of the screw and achieves uniform heating and mixing during this process, allowing the slices to be completely melted into a polymer melt with certain fluidity.
The melt is precisely measured in the metering section of the extruder and then filtered through a filter screen to remove any possible impurities and unmelted particles, ensuring the purity of the melt.
Spinning
The filtered melt is extruded from the small holes of the spinneret to form fine filaments. The number of holes and the diameter of the spinneret are selected according to the specifications and requirements of the product.
The extruded filaments undergo heat exchange with the high-speed flowing cooling air in the spinning corridor, rapidly cool and solidify to form primary fibers. Parameters such as the temperature, humidity and wind speed of the cooling air have a significant impact on the structure and performance of the fibers and need to be precisely controlled.
Stretch
The strength of primary fibers is relatively low, and their crystallinity and orientation are also not high. Therefore, the performance of the fibers needs to be improved through stretching. The stretching process is usually carried out on a stretching machine and adopts a multi-stage stretching method.
Fibers are stretched under heating conditions, and the stretching ratio is generally around 3 to 5 times. Through stretching, the molecular chains are oriented and arranged along the axial direction of the fibers, the crystallinity increases, thereby enhancing the strength of the fibers and reducing the elongation at break.
Network
The stretched fibers enter the network device, where they are subjected to the ejection of high-pressure air.
High-pressure air causes the fibers to interweave and entangle with each other, forming periodic network knots. The existence of network knots can enhance the bundling and cohesion of fibers, and improve the processing performance and application performance of fibers. Factors such as network pressure, the structure of network nozzles and the running speed of fibers will affect the quantity, size and uniformity of network nodes.
Winding
The polypropylene FDY network filaments processed by the network are wound on the tubes to form rolls of certain specifications and shapes. During the winding process, parameters such as winding speed, tension and winding Angle should be well controlled to ensure the quality of the winding, such as the flatness and tightness of the winding.
Throughout the entire technological process, it is necessary to precisely control and monitor the process parameters of each link to ensure the stable quality of polypropylene FDY network filament and meet the demands of different application fields.
Guangdong Modern High-tech Fiber Co., Ltd. is a professional manufacturer engaged in the development, production and sales of polypropylene fiber. Guangdong Modern High-tech Fiber Co., Ltd. has advanced production and research and development equipment, perfect process flow, scientific management framework, and a high-quality technical team, which is recognized as a national high-tech enterprise.